В октябре в порту Усть-Луга запущен в работу транспортно-конвейерный комплекс протяженностью 2 км, произведенный на кузбасском заводе горно-шахтного оборудования ООО "Объединенные машиностроительные технологии" (ОМТ), которое, по данным компании, остается единственным инвестором, реализовавшим в современной России проект полного цикла создания горных машин. Об основных вызовах, с которыми столкнулось отечественное горно-шахтное машиностроение, "Интерфаксу" рассказал генеральный директор ОМТ, член научно-технического совета Минэнерго РФ Владимир Добрыдин.
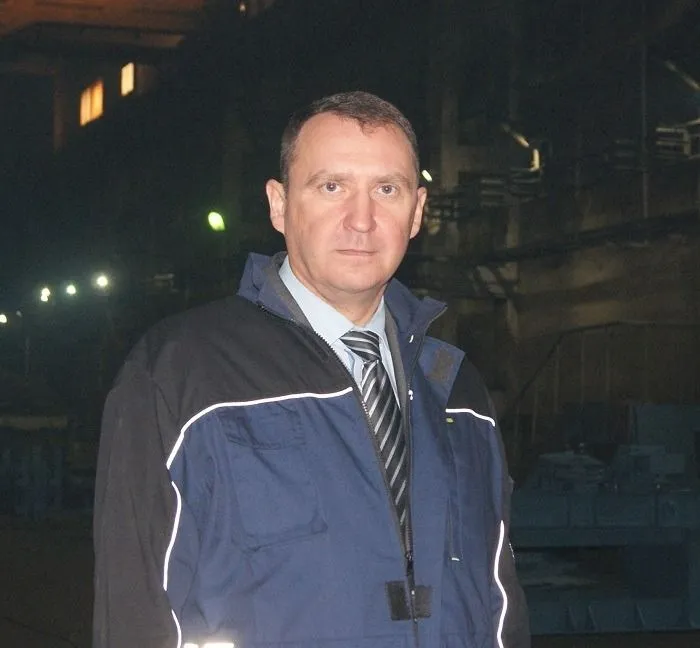
- Владимир Васильевич, в одном из выступлений вы заявили, что горно-шахтного машиностроения как отрасли больше нет - есть отдельные предприятия с определенными компетенциями и рынок, а отрасль, как регулируемая сфера деятельности, как цельное профессиональное сообщество, отсутствует. Можете прокомментировать это мнение?
- Производители горно-шахтного оборудования последние годы работают в очень непростых условиях: кризисы в угольной промышленности следуют один за другим и становятся все тяжелее, конкуренция с иностранными производителями горно-шахтного оборудования (ГШО) ужесточается.
Моментом прекращения горно-шахтного машиностроения как отрасли, по моему мнению, стало принятое примерно 1,5 года назад решение одной из крупнейших угольных компаний РФ провести закрытые торги, на которые российских машиностроителей не пригласили.
Сейчас участников рынка отечественного горно-шахтного машиностроения можно пересчитать по пальцам двух рук. При этом ряд предприятий существует только благодаря желанию конкретных предпринимателей развивать актив в сфере горного машиностроения. Эти инвесторы вкладывают немалые средства для увеличения технологических возможностей, при этом ассортимент продукции годами может оставаться практически неизменным. Вместе с тем, мы имеем примеры, когда машиностроительные активы, лишившись заинтересованного собственника, выходят на свободный рынок и самостоятельно не выживают.
Пора принимать системные комплексные решения, которые позволят заново сформировать горное машиностроение как отрасль. Начинать работу нужно с формирования четкой цели и последующей корректировки нормативной базы. Поскольку объединение разрозненных машиностроителей и создание эффективной отрасли – очень масштабный проект, для которого необходимо создать некий фундамент, систему гарантий и нормативное регулирование, то начать переговоры должно государство.
Мы живем в системе мировой интеграции, и здесь может быть только два варианта развития – либо должна идти консолидация активов, капиталов и основных фондов, как это происходит в Европе, либо предприятия должно поддерживать государство, как в Китае.
Консолидацию активов мы весьма наглядно могли наблюдать на примере крупнейших немецких компаний, специализирующихся на выпуске горного оборудования, так, сначала на базе нескольких заводов была сформирована компания Deutsche Bergbau Technik (DBT), позже она стала частью Caterpillar. Другой пример - мировая отраслевая корпорация Joy, которая консолидировала британских производителей горного оборудования.
Самый свежий пример - консолидация польских производителей под брендом FAMUR, который объединил известных в России производителей оборудования GLINIK, Rybnik и прочих, по сути, став национальным производителем.
Считаю, российским производителям ГШО нужно ориентироваться на западных коллег - собственного пути у нас нет, но есть стандартные экономические решения и пока сохраняются компетенции. Пока же в России нет тенденции к консолидации бизнеса, отсюда и закрытие машиностроительных мощностей, которое мы наблюдаем.
Впрочем, даже вхождение в корпорацию под эгидой государства, не гарантирует отдельному заводу успешного сценария развития. Это подтверждает пример ООО "Юргинский машзавод", где недавно ввели конкурсное производство.
Альтернативой консолидации, теоретически, может стать выпуск эксклюзивной продукции, однако фактически спроса на эксклюзив нет.
- А если говорить о кооперации предприятий горного машиностроения? В Кузбассе в течение нескольких лет на разных площадках неоднократно заявлялось о ее необходимости для повышения конкурентоспособности отечественных производителей ГШО и выпуска продукции в рамках импортозамещения. По Вашему мнению, удалось ли на практике наладить такое взаимодействие производителей ГШО?
- К сожалению, этого не произошло, и большая часть заявленных планов так и осталась на бумаге. Тем не менее, машиностроителям удалось достичь определенных результатов в части импортозамещения. Так, например, на российском рынке представлены ленточные конвейеры только отечественного производства. Но и при этом ряд их компонентов только импортные.
Если говорить об открытой угледобыче, то отечественные производители активно изготавливают навесное оборудование к бульдозерам и экскаваторам. Растет доля отечественных экскаваторов (производитель – "УЗТМ-Картэкс"). Рост обусловлен более выгодным, по сравнению с импортными производителями, ценовым предложением. Кроме того, сказывается влияние санкционного режима, а также тот факт, что этот производитель находится в составе крупной компании, у которой большие финансовые возможности.
Могу отметить эффективную работу созданного в 2015 году по инициативе Минэнерго РФ технического комитета по стандартизации "Горное дело". Его основная задача – разработка стандартов горно-шахтного оборудования. Это очень важно, особенно в ситуации, когда доля иностранных производителей на отечественном рынке достаточно велика.
- Кстати, насколько сильна конкуренция со стороны иностранных производителей ГШО?
- Думаю, больше половины рынка – примерно 70% сейчас приходится на долю польских производителей, объединенных под брендом FAMUR. Китайским производителям, которые еще 5-7 лет назад весьма активно заходили на наш рынок, российские потребители оказались неинтересны. Китайцы закрепились, главным образом, в сегменте крепей для угольных пластов средней мощности и в настоящее время скорее обозначают в России свое присутствие и поддерживают его, время от времени поставляя некоторым угольным компаниям Кузбасса крупное оборудование. Но все это разовые сделки, не системные, тем не менее, охватывающие до 20% уменьшающегося рынка. Системно присутствуют на рынке российского и кузбасского ГШО только польские производители. И только10% приходятся на российских производителей.
Что касается причин стремительного сокращения рынка ГШО, оно обусловлено приоритетом открытого способа добычи угля, соответственно, объемы добычи подземным способом (из шахт – ИФ) сократились. При этом за счет новых технологических решений на шахтах стало меньше очистных забоев. В итоге рынок сжался до 5-6 очистных комплексов в год против 10-15 комплексов 10 лет назад.
- Значительную долю бизнеса производителей горно-шахтного оборудования всегда составляли ремонты и оказание сервисных услуг. Как сейчас можно оценить конкуренцию со стороны сервисных структур самих угольных компаний?
- Почти все угольщики уже распродали свои машиностроительные активы. У некоторых компаний они еще есть, но, по моим данным, им сейчас как раз подыскивают покупателя. На этом фоне возрастает спрос на услуги специализированных компаний горного машиностроения по ремонту и модернизации.
- Владимир Васильевич, по Вашему мнению, какой стратегии стоит придерживаться сейчас машиностроителям, чтобы не только выжить, но и развиваться?
- Необходимо осваивать новые виды продукции, выходить на новые рынки, что и делает ОМТ. Так, например, последний год мы крайне мало работали для угольщиков. Два крупнейших контракта, которыми мы занимались – это производство транспортно-конвейерного комплекса для порта Усть-Луга, а также поставка конвейерно-транспортной системы для Жайремского горно-обогатительного комбината (Карагандинская область, один из основных производителей марганцевого концентрата в Казахстане, ТОО "Казцинк").
И, если продукцию для предприятий добывающих отраслей мы выпускаем уже давно, то в создании портовой инфраструктуры опыт небольшой. В этой сфере есть своя специфика: колоссальные требования к надежности и производительности оборудования и нюансы в обработке поверхностей.
Кстати, в порту Усть-Луга наш транспортно-конвейерный комплекс протяженностью 2 км запущен в работу 8 октября, 13 октября была успешно завершена загрузка первого судна - CL Beijing, ходит под флагом Hong Kong - грузом железорудного окатыша.
В перспективе ОМТ намерены работать над тем, чтобы увеличивать свое присутствие на рынке оборудования для горнорудной и химической отраслей, российских портов - мы рассматриваем варианты сотрудничества с портами Дальнего Востока и черноморскими.
С рынка угольной промышленности уходить мы не намерены и также планируем расширять здесь присутствие. Но, если раньше мы взаимодействовали, главным образом, с шахтами, то сейчас методично и целенаправленно работаем над тем, чтобы поставлять продукцию также и предприятиям, которые добывают уголь открытым способом. ОМТ уже выпускает некоторые элементы продукции для них – например, заготовки ковшей экскаваторов. Кроме того, активно пропагандируем применение конвейерно-транспортных систем для открытых горных работ (ОГР), которые при сопоставимых капвложениях гораздо выгоднее перевозок автотранспортом.
Также мы продолжаем работать над локализацией выпуска комплектующих для ряда немецких машиностроительных компаний на нашем заводе в Киселёвске. Так, уже выполняем заказы для ThyssenKrupp. Есть принципиальное соглашение с крупной европейской компанией о локализации производства металлоконструкций на нашем предприятии. Напомню, наряду с заводом в Киселевске в состав ОМТ входит конструкторское бюро в Москве на базе созданного в 1935 году "Гипроуглемаша".
- Сильно ли повлияла пандемия коронавируса на работу ОМТ? Как это скажется на финансовых результатах компании в 2020 году?
- Ограничительные меры, введенные в связи с коронавирусом, к сожалению, оказали очень сильное влияние на нашу работу. Так, в одночасье в апреле рухнули выстроенные логистические цепочки, на их восстановление мы потратили два месяца. Как это выглядело на практике? Скажем, своевременно на предприятие не поставили металл. В результате, с учётом технологического цикла, с выпуском продукции мы опоздали на три месяца. Оборотные средства вложены, а их возврат оказался отсрочен. Потеряли много времени и, значит, не выполнили какие-то заказы, за которые могли взяться и, по факту, потеряли в деньгах.
Кроме того, есть объективная необходимость в присутствии наших специалистов на объектах заказчиков в ключевые моменты – в ходе шеф-монтажа, пусконаладочных работ, а в этом году это не всегда было возможно. Так, например, Казахстан закрыл границы и до сих пор не открыл их. В итоге пришлось вести монтаж оборудования на ГОКе в режиме видеоконференции, а это повлекло временные издержки, сбои в работе оборудования, необходимость исправления ошибок, и, как следствие, задержку платежей.
Но, в этом году, в отличие от прошлого, мы ожидаем прибыль - это обусловлено тем, что сейчас произошла фактическая отгрузка продукции, которая была изготовлена в прошлом году и лежала у нас на складах.